Kleje do zabezpieczania gwintów: rzeczy, których nie wiesz, a powinieneś
W zakładzie MRO ważne jest, aby procesy produkcyjne przebiegały płynnie, a produkty były wytwarzane wydajnie i skutecznie. Chociaż urządzenia blokujące były tradycyjnie idealnym rozwiązaniem do ochrony nakrętek i śrub, kleje do zabezpieczania gwintów oferują lepsze, długoterminowe rozwiązanie, które usprawnia sprzęt i procesy. Jednak niektóre błędne przekonania mogą uniemożliwić korzystanie z nich w zakładzie.
Poznaj kleje do zabezpieczania gwintów i dowiedz się, w jaki sposób mogą one pomóc Twojemu zakładowi w porównaniu z urządzeniami blokującymi.
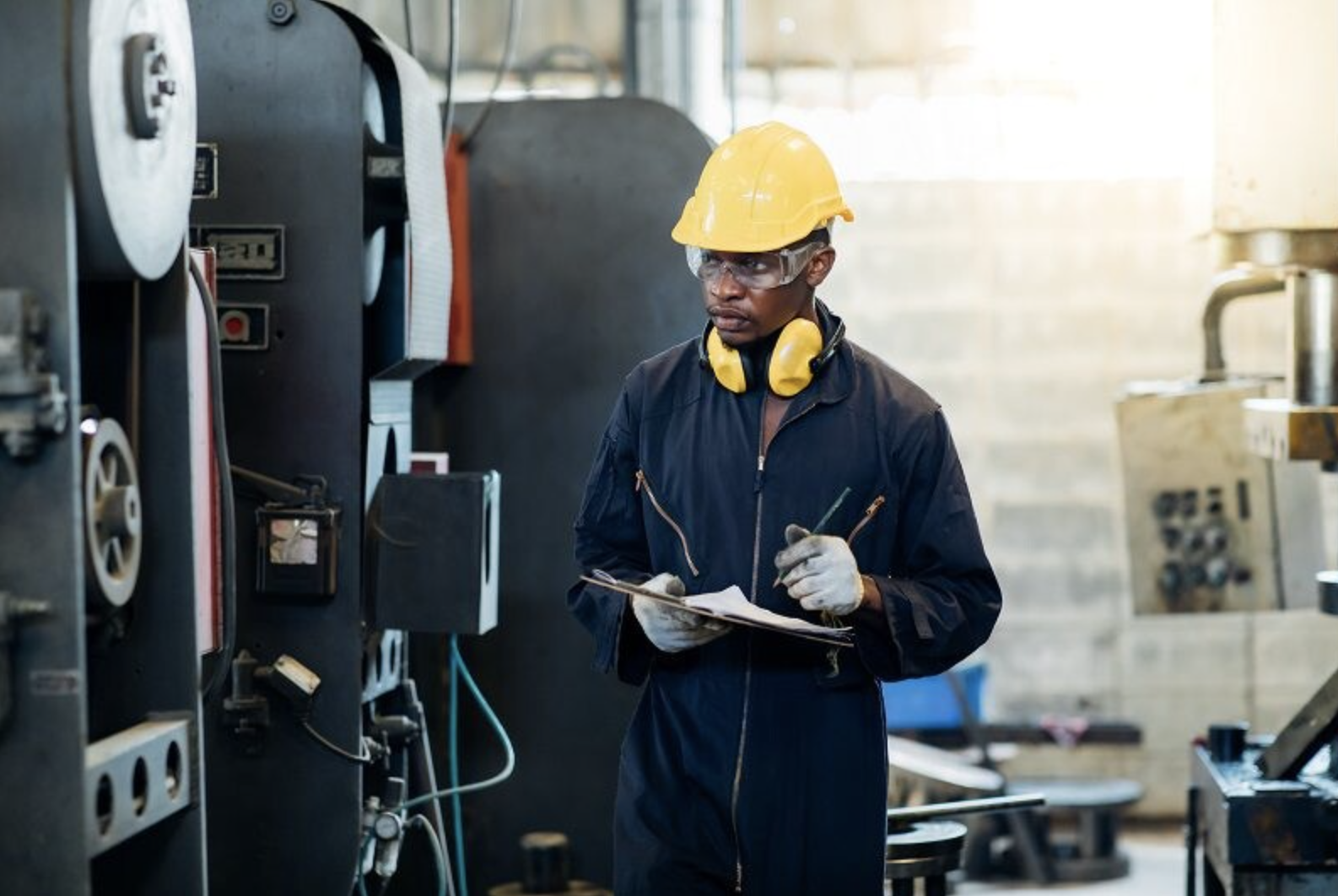
Błąd #1: Kleje do zabezpieczania gwintów są przeznaczone wyłącznie do stałego użytku
Kleje do zabezpieczania gwintów są nakładane na nakrętki i śruby w celu tłumienia drgań sprzętu i ochrony przed korozją spowodowaną przenikaniem wilgoci. Ponieważ tworzą one termoutwardzalne wiązanie z tworzywa sztucznego, które jest mocniejsze niż nakrętka nylonowa, wielu producentów uważa, że wiązanie to jest trwałe i nie można go usunąć w razie potrzeby.
Prawda: w rzeczywistości kleje do gwintów są dostępne w kilku opcjach, w tym usuwalnych. Kleje te można usunąć za pomocą prostego narzędzia ręcznego i niekoniecznie tworzą trwałe wiązania.
Błąd #2: Kleje do zabezpieczania gwintów nie są dostępne w różnych gradacjach
Chociaż wielu producentów wie, czym są kleje do gwintów, często myślą, że są one dostępne tylko w jednej gradacji. Prawdopodobnie przyzwyczajeni do szerokiej gamy kształtów i rozmiarów środków do zabezpieczania gwintów, takie postrzeganie może odwrócić ich od ich stosowania, myśląc, że nie są one dostosowane do konkretnych przypadków użycia.
Prawda: Kleje do zabezpieczania gwintów są dostępne w różnych zakresach dla wielu zastosowań. Na przykład, kleje do gwintów o niskiej wytrzymałości są przeznaczone do wszystkiego poniżej ¼, a nawet bardziej miękkich metali, takich jak aluminium. Ta zdolność pozwala producentom na ich szybkie usunięcie po aplikacji, jeśli zajdzie taka potrzeba. Kleje do gwintów są również dostępne w formułach o wysokiej wytrzymałości do bardziej trwałych zastosowań.
Błąd #3: Kleje do zabezpieczania gwintów zwiększają koszty zakładu
Producenci są zaznajomieni z klejami do gwintów i prawdopodobnie mają je w swoich magazynach we wszystkich kształtach i rozmiarach. Chociaż mogą one ulec awarii lub zgubić się, ich wymiana w razie potrzeby jest niedroga i nie stanowi problemu. Dla porównania, początkowy koszt klejów do zabezpieczania gwintów może wydawać się droższy niż urządzeń blokujących i w rezultacie nie są oni zainteresowani ich stosowaniem.
Prawda: Chociaż kleje do zabezpieczania gwintów mogą początkowo kosztować więcej, umożliwiają one obiektom obniżenie ogólnych kosztów w następujący sposób:
- Mniejsze prawdopodobieństwo wypadków: Urządzenia blokujące z natury zawodzą z powodu wibracji ciężkiego sprzętu, co może powodować odłączenie się sprzętu od gąsienicy i prowadzić do wypadków przy pracy. Ponadto awarie urządzeń blokujących na sprzęcie mogą stwarzać zagrożenie w miejscu pracy. Kleje do gwintów eliminują te problemy;
- Ograniczona konserwacja sprzętu: Nawet w przypadku stosowania urządzeń blokujących, nakrętki i śruby nie mają stuprocentowego kontaktu metal-metal. W rezultacie powietrze i wilgoć mogą przenikać i powodować korozję. Z czasem korozja może spowodować zatarcie nakrętki i śruby, utrudniając demontaż sprzętu i wymagając kosztownej konserwacji i naprawy. Kleje do zabezpieczania gwintów mogą zapewnić 100-procentowy kontakt w celu ochrony przed korozją;
- Zwiększona wydajność zakładu: Zakłady często mają całe magazyny poświęcone urządzeniom blokującym o różnych kształtach i rozmiarach. Kleje do zabezpieczania gwintów nie wymagają dużych powierzchni magazynowych i pozwalają na bardziej efektywne wykorzystanie przestrzeni zakładu. Można je łatwo włączyć do zestawu narzędzi na potrzeby na miejscu, oszczędzając producentom czas potrzebny na poszukiwanie odpowiednich urządzeń blokujących dla konkretnej nakrętki i śruby. Ponadto, jeden produkt może być stosowany do nakrętek i śrub o różnych rozmiarach, co dodatkowo upraszcza produkcję. Kleje do zabezpieczania gwintów pomagają stworzyć proaktywne podejście do napraw konserwacyjnych w zakładzie;
- Zwiększony przebieg produktu: W przypadku klejów do zabezpieczania gwintów wystarczy minimalna ilość produktu. Na przykład mała butelka o pojemności 50 ml może być użyta 800 razy w porównaniu z urządzeniami blokującymi nakrętki i śruby 3/8, co pomaga obniżyć koszty zapasów.
*Na podstawie wewnętrznych testów ekspertów.
Dlaczego warto wybrać kleje do zabezpieczania gwintów Born2Bond™ firmy Bostik?
Chociaż środki do zabezpieczania gwintów były w przeszłości popularną opcją konserwacji elementów złącznych, kleje do zabezpieczania gwintów oferują wyjątkowe zalety. Oprócz tego, że pozwalają zespołom konserwacyjnym działać proaktywnie, a nie reaktywnie, ujednolicają proces montażu, zapewniając, że cały sprzęt działa na tym samym poziomie wydajności. Ponadto oferują odporność na wibracje i korozję. Kleje do zabezpieczania gwintów Born2Bond firmy Bostik są:
- Dostępne w różnych gatunkach i lepkościach dla lepszej elastyczności;
- Jednoskładnikowe dla łatwości użycia;
- Odporne na olej dla lepszej wydajności;
- Wyposażone w technologię bez podkładu, która może być stosowana na nieaktywnych metalach, takich jak części platerowane, stal nierdzewna, cynk, czarny tlenek i aluminium.