Kleje na bazie wody to jedna z wielu technologii dostępnych obecnie na rynku do łączenia substratów. Są one stosowane w wielu branżach, ale szczególnie w etykietowaniu papieru, obróbce drewna, motoryzacji i tekstyliach, oferując wiele korzyści dla użytkowników i środowiska.
Aby zrozumieć zalety klejów na bazie wody i dlaczego mogą one być odpowiednie do danego zastosowania, ważne jest, aby zobaczyć, jak działają, ocenić różne składy chemiczne i zidentyfikować najlepsze praktyki konserwacji i obsługi podczas korzystania z tych klejów.
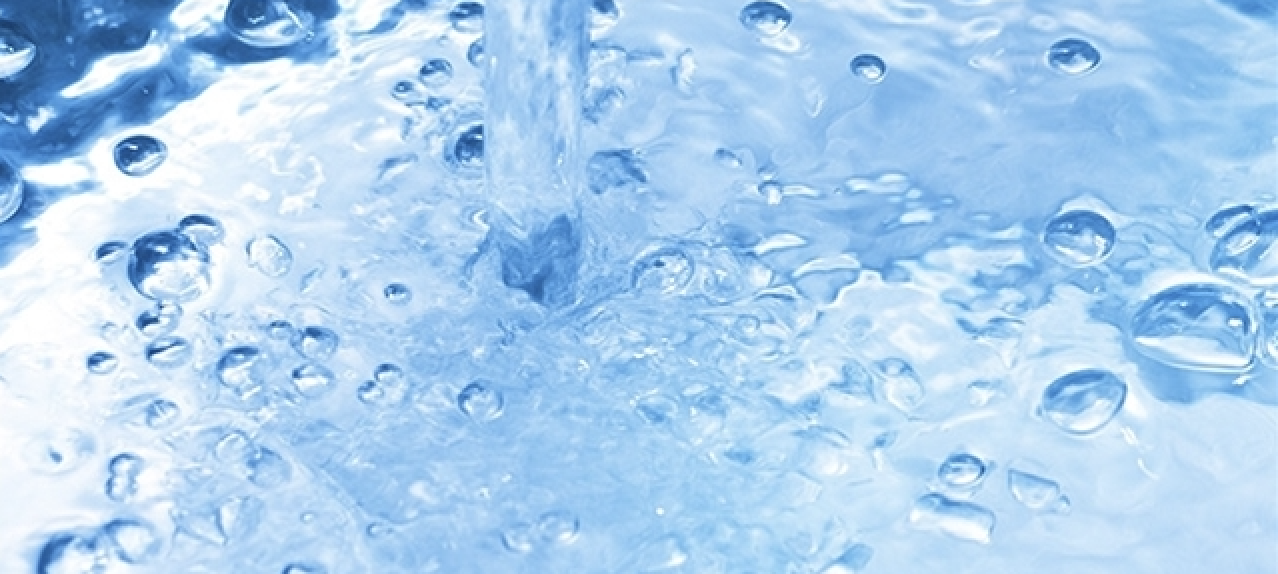
Czym są kleje na bazie wody?
Dostarczane jako wstępnie zmieszane lub suche roztwory – które są następnie mieszane z wodą przed aplikacją – kleje na bazie wody są nakładane w postaci płynnej, a woda działa jako nośnik zapewniający prawidłowe pokrycie podłoży.
Parowanie lub wchłanianie wody do podłoży pozostawia podstawę kleju, umożliwiając mu utworzenie wiązania, dlatego ważne jest, aby co najmniej jedno z podłoży było porowate, umożliwiając ucieczkę lub wchłanianie wody. Ponieważ proces ten może trwać kilka godzin, w zależności od składu, wymagana jest dobra przyczepność, aby utrzymać początkowy kontakt między podłożami. Dodatkowo proces może wymagać suszenia w piecach.
Płynny charakter kleju sprawia, że niektóre kleje wodne są bardziej podatne na wilgoć i nadmiar wody, co może niekorzystnie wpływać na wydajność klejenia poprzez dodatkowy czas utwardzania i zmniejszoną integralność wiązania. Ponadto wiele rodzajów klejów wodnych ma ograniczony okres trwałości w porównaniu do innych klejów.
Mimo to baza kleju ułatwia czyszczenie sprzętu, a w niektórych przypadkach ułatwia działania środowiskowe, np. umożliwiając łatwe mycie i ponowne wykorzystanie szklanych butelek oznakowanych i połączonych klejem na bazie wody, z myślą o gospodarce o obiegu zamkniętym.
Technologie klejenia na bazie wody
Zarówno syntetyczne, jak i naturalne polimery pochodzenia roślinnego (dekstryna i skrobia) oraz białkowego (kazeina) mogą być stosowane jako baza dla tych klejów.
- Każda opcja ma specyficzne właściwości, które wpływają na to, w jaki sposób produkt może być używany i do jakich zastosowań:
- Kleje na bazie dekstryny i skrobi: popularne w przemyśle papierniczym, kleje te są bardzo mocne, gdy są stosowane z określonymi materiałami, ale ze względu na ich bazę roślinną mogą ulec rozkładowi pod wpływem wody. Są one prawdopodobnie najbardziej przyjazne dla środowiska spośród klejów mokrych, ponieważ ulegają biodegradacji i nadają się do kompostowania;
- Kleje na bazie kazeiny: zapewniają silne wiązania, ale o stosunkowo długim czasie utwardzania; kleje te są wodoodporne i mogą być odporne na wodę kondensacyjną (CWR) i wodę lodową (IWR), dzięki czemu idealnie nadają się do etykietowania szklanych butelek w przemyśle napojów;
Kleje na bazie syntetycznej: są uważane za bardziej nowoczesne; mogą tworzyć silniejsze wiązania z większą możliwością dostosowania, dzięki czemu syntetyki nadają się do bardziej wymagających zastosowań i środowisk. Mają również dłuższy okres trwałości niż kleje naturalne.
Niezależnie od tego, czy są to kleje syntetyczne, czy naturalne, polimery stanowią szkielet kleju i zapewniają jego wytrzymałość i odporność chemiczną. Każdy klej zawiera plastyfikatory, które zmiękczają i poprawiają elastyczność, podczas gdy inne składniki przyczyniają się do przetwarzania i właściwości wiążących klejów na bazie wody.
Zalety klejów na bazie wody
Kleje wodne są tańsze w produkcji niż większość innych klejów.
Nie zawierają rozpuszczalników, mogą być również stosowane w obszarach niewentylowanych, co czyni je łatwym wyborem dla użytkownika, a także opcją przyjazną dla środowiska. Ich ekologiczne właściwości są dodatkowo wzmocnione przez aplikację w temperaturze pokojowej – zwykle około 21°C – 25°C – co pomaga użytkownikom zmniejszyć zużycie energii. Co więcej, wiele rodzajów klejów wodnych zawiera polimery pochodzenia organicznego, dzięki czemu są one idealne dla firm poszukujących produktu naprawdę przyjaznego dla środowiska.
Czyszczenie jest również szybkie i łatwe: wystarczy woda, aby zmyć klej z maszyn i urządzeń, ograniczając przestoje w produkcji i dodatkowo zwiększając zyski.
O ile nie są bezpośrednio narażone na działanie wody lub wilgoci, kleje wodne zapewniają mocne wiązanie. Jednak, jak wspomniano powyżej, niektóre, zwłaszcza kazeiny, mogą oferować odporność na wodę kondensacyjną (CWR) i wodę lodową (IWR), co czyni je idealnymi do zastosowań związanych z etykietowaniem szklanych butelek.
Producenci wybierający kleje na bazie wody muszą jednak wziąć pod uwagę dłuższy czas schnięcia i ograniczony okres trwałości, a także potrzebę starannego przechowywania i transportu klejów na bazie wody, aby uniknąć marnotrawstwa.
Przemysłowe zastosowania klejów na bazie wody
Ze względu na proces utwardzania obejmujący parowanie lub absorpcję wody, sektory przemysłowe najbardziej odpowiednie dla klejów na bazie wody obejmują stosowanie porowatych podłoży:
- Zastosowania papiernicze, w tym etykietowanie, bindowanie, tektura falista, produkcja kopert i znaczków;
- Tkaniny do zastosowań higienicznych;
- Podłogi i produkty wnętrzarskie w przemyśle motoryzacyjnym i transportowym;
- Obróbka drewna i zastosowania meblarskie;
- Sektor tekstylny i ręczników, np. do produkcji rolek toaletowych.
Konserwacja i czyszczenie klejów na bazie wody
Kleje na bazie wody mogą oferować stałą wydajność przetwarzania i łączenia. Jednak częstym problemem są siły odśrodkowe podczas przetwarzania, które rozpylają klej na sprzęt, prowadząc do przerw w produkcji i dodatkowego czyszczenia.
Jest na to sposób: sprawdź i dostosuj lepkość lub „grubość” kleju, jeśli to konieczne, a następnie wyczyść lub wymień wałki lub dostosuj prędkość wałków.
Przechowywanie kleju w odpowiedniej temperaturze – zwykle około 20°C – 25°C – powinno zapobiec jego nadmiernemu wychłodzeniu, co może zwiększyć lepkość i zmniejszyć elastyczność kleju, lub nadmiernemu nagrzaniu kleju, co może zwiększyć lepkość i ograniczyć jego trwałość.
Podczas obchodzenia się z klejem należy zawsze trzymać pokrywkę; zmniejsza to powierzchnię skóry, zapobiega zanieczyszczeniu i ogranicza rozwój drobnoustrojów.
Zapytaj eksperta o więcej informacji na temat klejów na bazie wody.